Die Vernetzung von Maschinen, Produkten und anderen am Produktionsprozess beteiligten Systemen ist Merkmal des Internet der Dinge. Durch den Einsatz von Sensoren können diese Verknüpfungen nun genutzt werden um Zustandsdaten von Maschinenkomponenten zu erfassen und sie mit Informationen aus Drittsystemen (bspw. ERP-, CRM-Systeme) zu kombinieren. Die Zielsetzung ist dabei auffällige, auf Störungen hindeutende Muster rechtzeitig erkennen und entsprechende Maßnahmen einleiten zu können.
Dieses Konzept der vorausschauenden Instandhaltung ist einer der Ansatzpunkte des Zukunftsprojektes Industrie 4.0, welches die Bundesregierung als eigenes Schlagwort für die vierte industrielle Revolution auf Basis des Internet der Dinge ins Leben gerufen hat. Der Fokus liegt darauf die Informatisierung, also die Erzeugung und Nutzung von Informationen, voranzutreiben um dem Ziel einer intelligenten Fabrik näher zu kommen.
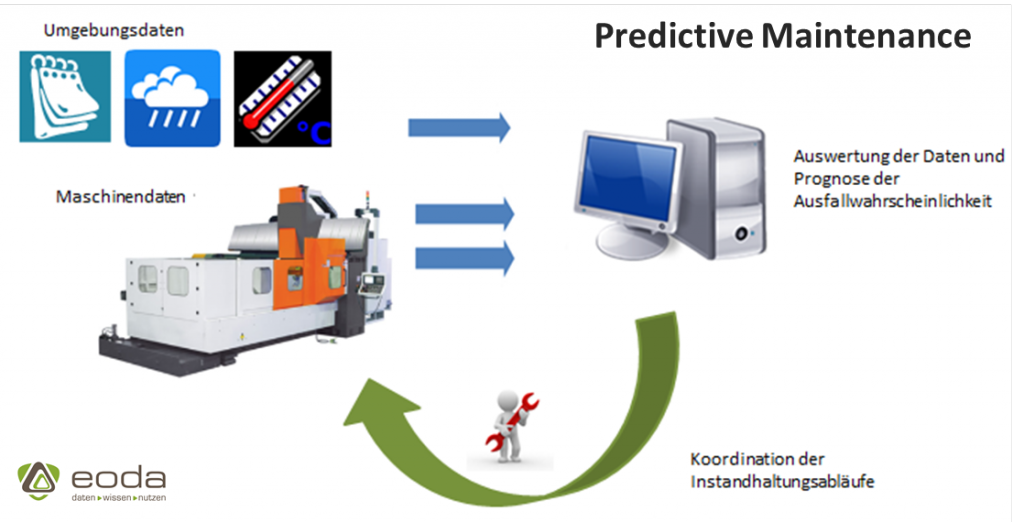
Predictive Maintenance als konkrete Anwendung
Eine sensorgestützte Ermittlung einer Vielzahl an Maschinendaten, sowie die Speicherung und Analyse dieser Werte schafft deutlich verbesserte Prognosemöglichkeiten über den Zustand der Industrieanlagen, und den Grundstein für eine höhere Planungssicherheit und eine effizientere Strukturierung von Reparatur- und Wartungsarbeiten. Die Produktivität steigt, indem Ausfallzeiten und damit verbundene Produktionsengpässe reduziert werden. Eine vorausschauende Instandhaltung ist der Schlüssel, um Nutzungsvorräte besser einschätzen und verwenden zu können.
Verschleißerscheinungen werden prognostiziert und es besteht die Möglichkeit, rechtzeitig die notwendigen Maßnahmen für eine Überholung des betroffenen Teils einzuleiten. Die notwendigen Instandhaltungsfachkräfte können informiert und die benötigten Ersatzteile bestellt werden. Der Zeitbedarf für den Reparaturprozess kann durch diese Maßnahmen drastisch reduziert werden.
Diese Form der detaillierten Maschinenzustandsanalyse bietet auch die Chance Verbesserungspotentiale an einzelnen Teilen frühzeitig erkennen und nutzen zu können.
Win-Win Situation für Anbieter und Anwender
Dabei entscheidend ist, dass parallel zu dem wachsenden Einfluss technischer Anlagen in nahezu allen Branchen auch Instandhaltungsdienstleistungen stetig an Bedeutung gewinnen und mittlerweile ein Milliardengeschäft darstellen. Im Zuge dieser Entwicklung hat auch ein Umdenken in der Branche stattgefunden. Die Zeiten eines ausschließlich reaktiven Instandhaltens im Anschluss an einen Störungsfall sind vorüber. Zu deutlich sind die Vorteile, die eine vorausschauende Wartung an sich oder zumindest als Ergänzung zum reaktiven Vorgehen bietet.
Aus Sicht der Anbieter von Maschinen und industriellen Anlagen bieten sich echte Wettbewerbsvorteile:
- Nutzung der Instandhaltung als strategisches Mittel
- Predictive Maintenance als Differenzierungsmerkmal
- Kundenzufriedenheit durch höhere Maschinenverfügbarkeit
- Kundenbindung durch einen verbesserten After-Sales-Service
- Optimierter Ressourceneinsatz in der Wartung und Ersatzteil-Logistik
Auf Anwenderseite sind die zuvor benannten Vorzüge des Predictive Maintenance Konzeptes Aspekte die Kosten senken und Kundenzufriedenheit durch eine möglichst verzögerungsfreie Auftragsabwicklung schaffen können.
R als Universalwerkzeug für Predictive Maintenance
Die Statistik Software R ist hierbei eine der besten Alternativen im Bereich der Datenanalyse und somit besonders geeignet für den Einsatz im Rahmen von Predictive Analytics. Diese Eignung leitet sich ab aus der hohen Leistungsfähigkeit von R, seiner Flexibilität und vor allem seinem enormen Funktionsumfang, der bei der zuverlässigen Auswertung unterschiedlichster Maschinen- und Umgebungsdaten einen entscheidenden Vorteil darstellen kann.
Einsatzmöglichkeiten von Predictive Maintenance
Handelt es sich bei einer Produktionsanlage um den zentralen Bestandteil der Unternehmenswertschöpfung ist die genaue Kenntnis über den Maschinenzustand und seine Einsatzsicherheit elementar. Diese Notwendigkeit wird nochmals verstärkt, wenn Umstände vorliegen die ein rein reaktives Vorgehen als ökonomisch fatal erscheinen lassen. Industrieanlagen in schwer erreichbaren Regionen, besonders zeitaufwendige Instandhaltungen, oder auch eine problematische Ersatzteilbeschaffung sind als Beispiele für solche Umstände zu nennen, die einer möglichst vorausschauenden Planung bedürfen
Ein Windkraftanlagenbauer möchte seinen Kunden einen möglichst zuverlässigen und schnellen Service bei der Wartung und Reparatur ihrer Anlagen bieten. Um dies zu gewährleisten setzt er auf Predictive Maintenance in Form einer gezielten sensorgestützten Auswertung der Maschinendaten wie Schwingungen, Resonanzen oder Betriebstemperaturen. Dadurch können zukünftige Störungen früh erkannt, der Kontakt mit dem Anlagenbetreiber gesucht und passende Maßnahmen in die Wege geleitet werden ehe größere finanzielle Verluste durch einen längerfristigen Ausfall drohen.
Für Instandhaltungsdienstleister kann es ein entscheidender Vorteil sein detaillierte Informationen über das Ausfallrisiko bestimmter Maschinenteile zur Verfügung zu haben. Dies erleichtert das Vorgehen bei einem Einsatz und kann ein Differenzierungsmerkmal im Vergleich zu den Wettbewerbern der Branche darstellen.
Ein Getränkelieferant möchte eine Aussage darüber, wie zuverlässig seine Abfüllanlage in Zukunft sein wird. Anhand von Einflussvariablen, wie der vergangenen Beanspruchung, Maschinendaten oder der Intensität der geplanten zukünftigen Nutzung kann eine Prognose getroffen werden mit der ein überraschender Ausfall in einer entscheidenden Produktionsphase verhindert werden kann.
eoda unterstützt als Spezialist im Bereich der Datenanalyse Unternehmen bei angestrebten Veränderungen im Umgang mit der Instandhaltung. Durch eine Analyse der ausgegebenen Maschinendaten, sowie eine Einbeziehung der relevanten Umgebungsdaten lassen sich, ohne eine aufwendige Inspektion der Maschine, Aussagen über den Zustand der Anlage und ihrer Ausfallwahrscheinlichkeit treffen.
Hier entlang.