Benefit
Ability to make predictions about machine failures
Kind of data
Sensor data with historical error and fault messages
Methode
Deep learning
Predictive maintenance with deep learning algorithms in industry 4.0
Challenge
An international operating mechanical engineering company is pushing ahead with the digitalization of its production. One starting point: The data-supported optimization of maintenance. The available database for this purpose contains, among other things, sensor readings that contain error and malfunction messages at different time intervals. This provides the machine manufacturer with comprehensive information, since more than one hundred machines, each with more than 250 sensors, continuously supply data.
Aim
The aim is to forecast machine failures at an early stage so that preventive measures can be initiated for predictive maintenance. The data science specialists at eoda will use the analysis of sensor readings to identify processes that can lead to machine failure.
Solution
Solution
The key to reliable prediction of machine failures lies in the detection of recurring data patterns prior to historically documented machine failures and malfunctions. In this case, the data science specialists used a deep learning model. Deep learning, a method from the field of machine learning, can use artificial neural networks to analyze large amounts of data of varying complexity on several levels in order to identify complex relationships. The more data is used to train the deep learning model, the more precise the results become, because the learning algorithm optimizes itself in the analysis process.
Based on this method, eoda has developed a multi-label classification model to register the occurrence of specific error messages from sensor data. Several error messages were divided into classes and performed for a descriptive analysis of specific time intervals. For this, the programming language R was chosen, which is recommended for the conduct of a proof of concept, especially for a large number of individual variables.
The measured values of the sensor data from different sources were aggregated, scaled and transformed in order to create a uniform standard for data comparison. Only this step made it possible to analyze the data, as each sensor measures at different intervals and at different times. These measured values had to be processed in such a way that the data could be transferred from different sources of information into a uniform format and were also on one basis across all machines.
The next step was to create a meaningful division of information into training, test and validation data. Since the errors in the data were distributed unevenly, it was necessary not only to take random samples, but also to work with downsampling and upsampling in order to obtain a meaningful distribution of errors and non-errors. The resulting learning effect through training, testing and verification is the most important step in model building – especially to avoid under- and overfitting.
Due to the big data scenario and a long calculation time, the cloud-based workstation Amazon Web Services (AWS) was included to speed up the process. With the first prototype different layer architectures could be determined and evaluated. Deviations due to the pre-processing phase were improved. In this case, the technical framework for the deep learning framework was provided by a Keras API written in Python, which provides an interface for the deep learning library TensorFlow.
In the last step, the evaluation of a classifier was calculated according to its relative frequency. For this purpose, a confusion matrix was created with a focus on cost minimization. The values readable from the matrix show the frequency of occurrence of feature combinations.
Result
Thanks to eoda’s deep learning model, the machine builder can make predictions about faults in industrial plants and proactively initiate the appropriate maintenance measures. This not only avoids expensive and unexpected breakdowns, but also makes it easier to achieve the specified production targets. This case is a successful example of how data and algorithms can form the basis for reliable and more profitable production.
By implementing the upstream proof-of-concept, it is not only possible to quickly determine important findings for answering individual questions, but above all to make statements about the feasibility and profitability of the specific use case. Only in the case of a positive assessment, the analysis model is implemented in the business processes.
Data-Driven Software:
YUNA – Data Science Platform
YUNA is the central platform for the development and control of digital, AI-supported projects. It combines BI functions with the possibility to use various models and scripts.
Learn more!
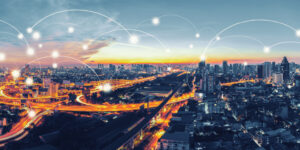
Use Cases:
Data Science in your industry
Optimized processes, time savings and cost reductions - these are the results when Data Science is used successfully.
Discover more use cases here and get inspired!
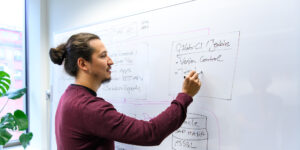
Data Science Infrastructure:
On Premise, Cloud or Hybrid
Design, implementation and support! We are the provider of resilient and reliable data-driven services. We also make your infrastructure ready for the digital challenges of the future!
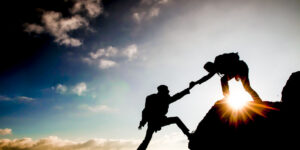
Data Projects:
From the idea to productive service!
Which use cases are particularly purposeful for you? How can knowledge creation succeed in your company? From the solution idea to the productive use of AI systems in your company: We create perceptible added value for you from data.